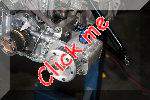 |
Time
for an update, albeit quite some time after the race in November 2007.
On the left is the new mounting for the oil scavenge pump, fitted to
the side of the engine to make it more rigid and save a little weight.
On the right is the new pedalbox and pedals. The link to run the clutch
cable off has been fitted and also a small bracket to mount the front
brake t-piece onto, sitting on the chassis tube just in front of the
front brake master cylinder. |
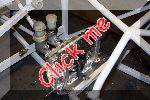 |
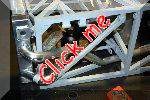 |
Another
major
change I made was to the water plumbing. The original was pretty
tightly wedged into the engine bay and hard to get out when working on
the car. It was also pretty unweildy so I decided to make the water
pipes run far more neatly and be easier to get out of the car. To do
this, we made some connections on the end of the radiator and in a few
other places, so the long pipes would come out in a few pieces. I
decided to run the hot return water on the other side of the engine,
down the exhaust side, as there was far more room. The cold water pipe
from the radiator also ran through the oil/water heat exchanger, which
fits nearly in the empty space behind the radiator. The new pipe going
into the back of the water pump is also hugely
neater than the old one. Instead of being crowded up against the
starter motor, there was just enough room to take it down inbetween the
engine mount on that side. |
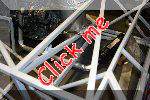 |
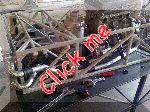 |
On
the left you
can see the rubber joins in the hot water return pipe, to allow it to
be removed from the engine bay with the engine still in place, and also
remove the engine from the car with only a one rubber join undone on
that side.
On the right you can see the long run down the back of the engine that
pipe makes, and to help support it, we welded a small tag onto it and
it goes under a bell housing bolt to stabilise it all.
There's also the new oil tank mounts, again to simplify things and make
it easy to remove. The chassis was also sand-blasted and coated with an
anti-rust paint.
If you look closely you can also see the simple radiator mounts we came
up with. There's two on the left and one on the right, to allow the
radiator to flex around a bit if it needs to. |
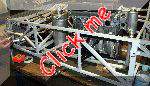 |
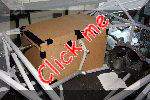 |
I
had to come
up with new footwell panelling, as the old one was pretty poor
and
very hard to work on. It took a lot of sitting around and thinking
about it, but the end result was well worth it. The panels are thin
aluminium and can be totally removed from the car in a couple of
minutes. The panels are held in place with small Nutserts, and they
lock together to make a strong unit. The top cover is also held in
place with Nutserts, but the long side closest to the engine slides
into a slot in the top of the vertical panel, again to make it fast
& easy to get into the footwell. |
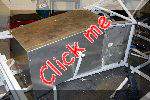 |
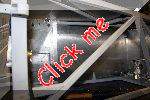 |
On
the left you
can see how the big vertical panel joins around where it intersects the
top part of the engine mount. With a little alloy sticky
tape, it
all holds together very neatly an is fuel/oil proof.
On the right is the new backrest panel. The old panel was made up from
two or three separate parts, and so a lighter & simpler
single-piece one was made. Also in that photo you can see the two
little tabs welded onto one of the chassis tubes with the holes in them
- they are the new fuel tank mounts, and again they are far more simple
and lighter than what it used to have. It'll also let the tank move a
bit if there's a crash, and not be bent and spit, and so let fuel out. |
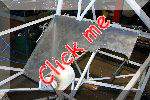 |
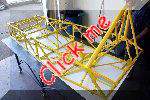 |
Like
the
Fraser, I decided to make the chassis a little more eye-catching, and
so it too is painted YELLOW now. I did the painting, and I discovered
I'm not very good at it! But multiple coats covered multiple sins,
shall we say. On the left is the freshly-painted chassis sitting on the
new floor panelling. Unfortunately the only suitable alluminium panel I
could get had a white coating, so that's how it now looks. Well, the
oil leaks show up quickly .....
On the right are the new side panels, and unlike the old panels they
aren't full of holes to let the hot engine bay air out. |
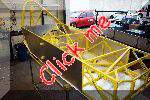 |
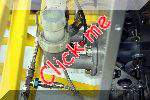 |
On
the left is the completed brake & pedalbox assembly. The new
pressure swtich fits in very neatly, though to get the brake line from
the master cylinder to the t-piece I had to use an odd-shaped fitting
to bring the line under the master cylinder to make it all work.
On the right, the engine slotted in nicely, with the new scavenge pump
position working well. The only hassle is getting the scavenge line
from the sump to the pump as the angles & distance don't leave
a lot of options. We ended up re-using the old line, but it wasn't good
and after the race I changed it for a much better solution - photo to
come. |
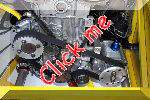 |
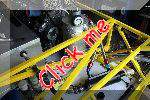 |
Nearly
there! On the left there's lots of little things that I've
done - On the top of the footwell box there's a rubber strip for the
Mikuni carbies to rub on, if need be. You can also see how the cold
water pipes run across the front of the car, and how the oil lines go
to/from the heat exchanger. The mounts for the oil tank are done, and
because the tank fits in so neatly all it needs is a few cable-ties to
hold it firmly in place.
On the right is how the diff slots into the back of the car, leaving
just enough room for it to move around and not hit anything. |
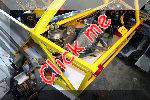 |
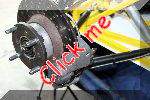 |
There
seemed to be enough spare time to do some extra work on the brakes, so
I bought a pair of AP Lockheed lightweight racing calipers for the
front, saving a full 4kg from the car because the old calipers were Mk1
Cortina and made from steel. The original brakes lines pretty much
bolted straight-up, which made a pleasant change from all the other
difficult modifications done on the car.
On the right is the new all-glass nose, which also weighs quite a lot
less than the old nose and is far more rigid, and also makes more
downforce. You can see the alloy plates bonded to the sides and that's
how it attaches to the car. In early 2008 we welded some nuts to the
inside of the support tubes so the bolts are also far easier to fit
than the old nose. |
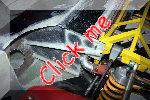 |
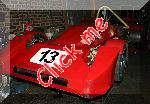 |
This
is the last photo of the car I took before the race meeting. I quickly
threw it together to see how it looks with the newly-painted engine
cover and nose.
So how did the race go?
On the right is the once-again broken gearbox mainshaft ...... read on
below as to what happened. |
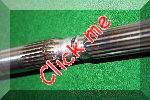 |